Rotary screw air compressors use of the rotary type positive displacement and are mainly and generally used for the replacement to the piston compressors, in the applications in industries and commercial things where there is a need for a large amount of air that is high pressure. There is another name for this rotary screw air compressor that is usually not used. It is also called a twin-screw compressor.
Any machine can get repaired or can temporarily or permanently wear out when it is used continuously or when they are not used for a long period of time. Some of these can be simple problems while some of them can be large problems. The large problems can only be solved by mechanics while the small problems can be troubleshot by anyone and can be repaired if they know the proper steps to do the reparation works on it. To prevent them from getting damaged and repaired there are some steps that have to be maintained and followed to get the machine running in good condition. Here are some of the steps that can be easily followed to have the rotary screw air compressor in good working condition.
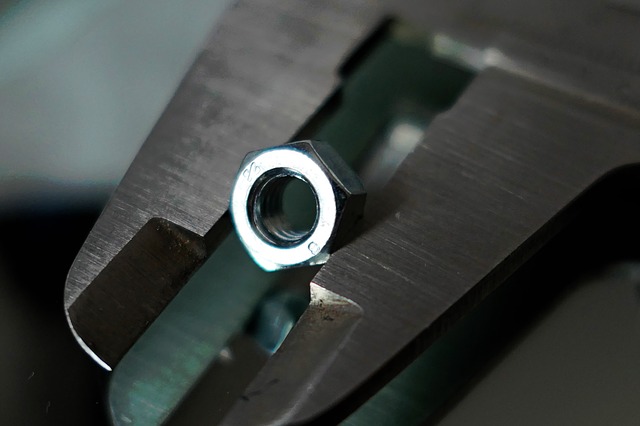
To prevent the damages, the main step is to check whether the rotary screw air compressor is working efficiently for a long span of working conditions and there will fewer times that the air compressor will be needing unscheduled repairs. With the different types of air compressors, you have like the high pressure one, the low-pressure one, or the screw air pressure compressor following the manual is the best way to know about the maintenance of the air compressor. Though they have the manual for each type of air compressors here are some of the most common parts for the maintenance of the rotary screw air compressor:
- Airends: The screw elements are also called as airends and here in this part the air compression happens. Airends are considered to be the main component in any rotary screw compressor. These can be easily damaged by the contamination, excessive heat, and screw compressor fluid that is dirty. To prevent add regular checking on to the airends of the rotary screw compressors. If there is the noise that is excessive and if there are vibrations, these can also that there can be some problems with the airends.
- Drive train: Drive train checking is also another important step. Check whether the drive train is correctly aligned and also check whether the gear drives are lubricated properly. For every 500 hours the tension between the V- belt drives must be checked and adjusted appropriately. If there are torn or frayed belts replace them as soon as possible or immediately.
- Filters: On a consistent basis, if the rotary compressor filers have to be replaced to prevent the premature wearing out. This will also ensure that there are less component contamination and airend wear. The recommended timing for the replacement of the in filters of the roast screw compressor is every twenty thousand hours. And the fluid filters must be changed or replaced every 1000 hours.
- Motor: The bearings of the motor have to be lubricated properly and before them wearing out they have to be replaced from time to time. The ampere draw also has to be monitored so that there the chances of overloading can be minimized or lessened. There has to be ventilation in the room. Hence check whether the room has sufficient ventilation. This can help the motor go to a long lifespan.
These are some of the simplest steps that can be followed for the easy maintenance of the rotary screw compressor.